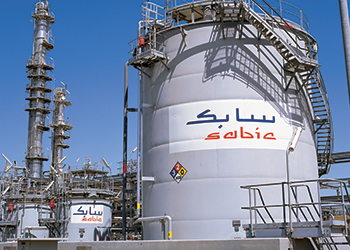

During the process, Sabic captures the recyclate from their packaging material and converts it into new plastic bags containing 50 per cent recyclate. Bags are then produced, together with Fardem and Morssinkhof, that do not compromise on quality
Four million plastic bags made with 50 per cent recycled material will be used to package polymer resin, thanks to a new ‘closed-loop’ collaboration launched between global petrochemical company Sabic, converter Fardem Packaging (subsidiary of Oerlemans Packaging) and recycling company Morssinkhof Rymoplast.
"Following our recent launch of certified renewable polyolefins, this is another example of Sabic’s commitment to sustainability and environmental protection. We strive to continuously create more sustainable business processes that create value into the future for society and the environment, based on the effective use of the resources available to us today", says Steven de Boer, director Innovation and Sustainability, Polymers. "In this particular project, downcycling is avoided, and a higher quality use of a waste stream is generated, with a 2nd life given in the same application," adds de Boer.
During the process, Sabic captures the recyclate from their packaging material and converts it into new plastic bags containing 50 per cent recyclate. Bags are subsequently produced, together with Fardem and Morssinkhof, that do not compromise on quality. These bags are then used to package selected Sabic resins.
Recycling company Morssinkhof Rymoplast collects the used plastic bags from a logistics service provider contracted by Sabic, and recycles them back into recycled plastic pellets. Rolf Morssinkhof of plastic recyclers Morssinkhof Rymoplast says, "We are very happy to be part of Sabic’s ‘bag to bag’ programme, which is ultimate proof that by collection of well sorted monostreams of plastic scraps, production of recycled raw materials for re-usage in the original application is possible.
"Sabic is setting the right example and challenging the plastics industry to take similar pragmatic actions. Morssinkhof Rymoplast, as one of the leading plastic recycling companies in Europe, is very prepared to support the industry in closing their loops with high quality recycled raw materials in PE, PP, PS and PET."
Fardem Packaging is then responsible for adding 50 per cent virgin material to 50 per cent of the recycled material, to make Sabic’s new plastic bags that weigh 100 grams and can carry 25 kg of plastic product. "To make the circular economy a success, co-operation between all parties in the chain is required. Fardem Packaging is ready to take their role and responsibility in this process", says Joan Hanegraaf, CEO Oerlemans Packaging (holding company of Fardem Packaging).
The short-term outcome of the ‘bag to bag’ project – up to 100 thousand tonnes of plastic per year could be transported from Sabic to its customers in recycled bags.
Meanwhile, Dell has announced progress with the expansion of its closed-loop recycled plastic supply chain, as well as introduction of reclaimed carbon-fibre source materials.
For this, Dell has partnered with supplier Sabic to recycle excess carbon fibre and scrap raw materials into new Dell products beginning in late 2015. Initially, select Latitude and Alienware products will contain recycled carbon fibre, with plans to expand across these two product portfolios in 2016.
Dell estimates that by partnering with Sabic, it will prevent 820,000 lb of carbon fibre from ending up in landfills. The recycled carbon fibre materials have an approximately 11 per cent smaller carbon footprint than simply using virgin carbon fibre. Since Dell began pioneering its closed-loop recycled plastics supply chain in January 2014, the company has recycled 4.2 million lbs of closed-loop plastics into enclosures for new Dell products.
These plastics were used in more than 30 flat panel monitor models and three Dell OptiPlex desktops available globally, with plans to scale across servers and other products in 2016. Dell’s process was certified by UL Environment as the first closed-loop supply chain, and continues to be the only one in the industry. Dell was also able to reduce its product carbon footprint via the closed-loop products by 11 percent and realized a cost savings over previous sources.
"The technology industry has a unique responsibility to help shift the world to a circular economy model, and Dell’s long standing investments in sustainable business puts us in a unique position to lead the way," says Trisa Thompson, vice president and chief responsibility officer at Dell. "We are always looking for collaborations that bring efficiencies to our business, and help our customers do the same."